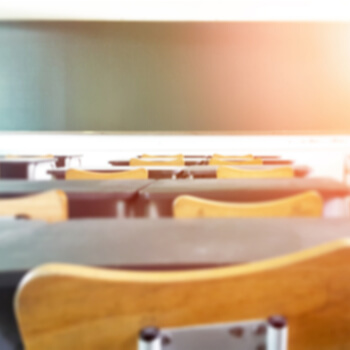
BLOG: Three Valuable Lessons from 20 years of Supply Chain Crisis Management
No two global crises are exactly alike. But, that doesn’t mean there aren’t patterns between them for procurement teams to learn from.
When a crisis like the COVID-19 pandemic strikes, few organisations are ever truly prepared. These events are global, powerful, and unforeseen. By their nature, the risk they represent is virtually impossible to mitigate completely. However ready you think you are, you will always face some amount of disruption.
But, that doesn’t mean procurement and supply chain risk managers can just sit by and wait for the next crisis to happen – far from it. Every crisis brings valuable lessons for the organisations and processes disrupted by it. By taking the time to reflect on these issues once the situation settles, organisations can reduce the impact and damage caused by the next one – wherever and whenever it strikes.
The Smart Cube has been helping businesses build resilient procurement and supply chain operations for two decades now, delivering powerful insights to help our customers mitigate supply chain disruption locally and globally.
During those years we’ve seen numerous major global incidents impact economies and bring entire markets to their knees. Here are three important lessons we’ve learned from them.
Lesson #1: National emergencies can become global threats faster than most of us imagine
Over the past two decades, the globalisation of markets, economies and supply chains has created an incredibly intricate web of dependencies. It’s a huge asset to companies right worldwide – enabling them to trade profitably with customers everywhere, access huge markets, and secure exactly what they need, whenever they need it, at the right price.
However, in many ways, these global supply chains and economies are like a house of cards. They’re incredible to behold, and have taken true skill and expertise to build. But, if just one card falls, the rest can easily topple, turning a relatively isolated event into a major international crisis.
Take a natural disaster like the 2008 earthquake in China, for example. While enormous in magnitude, most of the damage occurred in southwestern China. It would be easy to think that such an event wouldn’t have any major repercussions on companies outside of the country. However, this was certainly not the case.
The earthquake caused huge damage to agricultural land, limiting food supplies and driving up food prices across China. That impacted living wages in the country, an impact that had to be absorbed by export customers. Even companies whose suppliers in China weren’t physically disrupted by the earthquake soon found themselves feeling the impact of it – an impact that most failed to anticipate.
Lesson #2: Today’s ‘normal’ is tomorrow’s unacceptable
Times change, and as you forecast potential threats to your supply chain, you can only see what today’s lens will show you. If something isn’t considered a problem today, it’s very hard to recognise that it could easily become one tomorrow.
Look at the 2008 financial crisis, for example. It was triggered by the collapse of the US sub-prime mortgage market the year before. Looking back now, many of us are left scratching our heads wondering how sub-prime mortgages were ever allowed to exist, let alone be offered at the scale they were.
Hindsight is 20/20 of course, but this shows us the value of casting a critical eye over current operations and practices, and considering how what we do today may be invalidated in the future.
Ongoing issues like climate change are the perfect example of this. It’s highly likely that over the next two decades, major shifts in global logistics operations will need to happen in line with growing sustainability demands and regulations. Our children will probably be outraged at what we consider ‘normal’ today in terms of emissions and movement of goods.
Those with the foresight to consider how serious those shifts may be and challenge today’s normal will certainly be better set up to succeed when that change inevitably comes.
Lesson #3: The pace of disruption itself is increasing at an alarming rate
As the old adage goes, the only constant is change. However, today the pace of change is anything but constant. In the last 10 years alone, we’ve experienced major natural disasters, huge financial turbulence, massive geopolitical shifts like Brexit, major civil unrest, a global pandemic of unprecedented scale and severity, and much, much more.
For companies with international operations, these events are never-ending. Just as one comes to a close, another emerges in another location. For the teams and executives who must respond to these changes and safeguard supply chains, it’s no longer a case of if an unforeseen event will strike, but when, how severely, and for how long?
This is – or at least, should be – driving real change in how procurement and supply chain leaders think about risk. It’s no longer about preparing for events that may or may not happen, it’s about ensuring that operations can continue tomorrow, whatever challenge it brings.
That in turn is driving interest in new solutions to help monitor, tackle, and improve management of risk. A new generation of solutions offering ongoing risk monitoring and intelligence are supporting this shift, enabling teams to spot developing risks earlier, and start mitigating them faster.
Look back to look forward
We’ve heard the word ‘unprecedented’ thrown around a lot in 2020 and 2021. It’s an accurate description of the COVID-19 pandemic, but from a risk management perspective, it’s also dangerous.
The idea that there is no precedent for the challenges we’re tackling today undermines everything that expert risk managers have learned over the course of their careers. Yes, these are in many ways unique times and circumstances that we face, but there are lessons to be found in every crisis in recent memory – lessons that can help us mitigate the risk and disruption of the next global crisis.
Now more than ever, we must look back to look forward, learning from past disruption to build more resilient supply chains, ask difficult questions, and respond faster when the next crisis strikes.